Az Adidas új sportcipője robotokkal, szénszálakkal és 3d nyomtatással értelmezi újra a húrelméletet

Az Adidas új sportcipőjén nem kasmírgarbós ruhaipari dizájnerek és bangladesi gyerekmunkások dolgoztak, hanem sporttudományi szakértők, számítógépes tervezőmérnökök, és egy olyan gyártósori robot, ami 3d nyomtatóval és okosan elhelyezett szénszálakkal teszi egyszerre kényelmessé és strapabíróvá a cipőt.
Az elmúlt években a sport- és ruhaipari vállalatok is kiaknázták a 3d nyomtatás lehetőségeit. A sportcipőgyártók felismerték, hogy a szénszálas technológia rugalmasabbá teheti a cipők talpát. Ebből elsősorban a futók profitálhattak, mivel így a talpak extra lendületet és nagyobb sebességet biztosíthatnak futás közben. Az Adidas új cipője viszont nemcsak a cipő talpát, hanem a felsőrészét is stratégiai pontokon elhelyezett szénszálakból alakította ki.
Az Adidas a gyártástechnológiát Futurecraft Strung néven jegyezte be. (Az angol „strung” szó egyszerre jelent fűzést, feszítést és húrt.) Nem vadonatúj eljárásról beszélünk – az Adidas Futurecraft munkatársai tervezték az újrahasznosítható Loop edzőcipőket és a cég 3d nyomtatóval készült cipőtalpait is –, de mostanra odáig fejlődött, hogy már a cipők felsőrészét is ezzel készíthetik el.
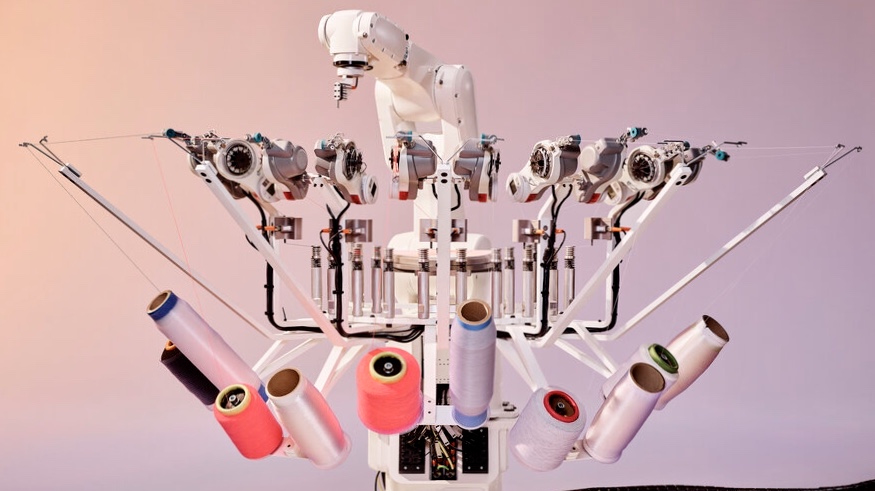
Gépi tervezés, de emberi igényekhez igazítva
Első pillantásra az Adidas Strung igen kaotikus benyomást kelt. A cipő talpa nyers instant tésztákat idéz, a teteje pedig olyan, mintha telibe trafálta volna a Pókember hálója, de a konstrukció gondos tervezés eredménye. Bár a gyártást végző, egyedi tervezésű robotok több mint ezer szénszálat fűznek keresztbe a cipő tetején – néha egészen elképesztő szögekben –, ezeket úgy alakították ki, hogy a lehető legkényelmesebb tartást biztosítsa a lábfejnek futás közben.
Gyártástechnológiai szempontból kétségkívül ez az Adidas legmodernebb cipője. A hagyományos futócipők felső részének szövetszálait általában vízszintes vagy függőleges kötéstechnikával dolgozzák ki, esetleg ezek kombinációjával; Nike Flyknit technológiája például kis négyzeteket köt. A Strung ezzel szemben több rétegben helyezi egymásra a különálló szálakat, ráadásul ezek nemcsak a távolságukban és a vastagságukban, hanem az erősségükben is különböznek.
A sarokrészen használt legvastagabb szálat csakis a sarokrészen használják, mert arra nehezedik a legnagyobb nyomás, így az ott futó szálaknak nem szabad megnyúlniuk. A lábujjakat körbevevő szálak viszont nemcsak vékonyabbak, hanem kevesebb is van belőlük, mivel ott kisebb a cipőre nehezedő erőhatás, és a ritkásabb szövet jobb szellőzést biztosít a lábfejnek.
A tervezés során az Adidas a futóktól begyűjtött adatok számítógépes elemzésére is nagy hangsúlyt fektetett. Az olyan viselkedési adatok, mint a futók sebessége, a futás helyszíne, a lábfej mozgása vagy a cipőre nehezedő terhelés vizsgálatával pontosabban meghatározhatták az egyes szénszálak helyét. A gyártást azonban nem bízták teljes mértékben a számítógépekre. A modellező szoftverek több lehetőséget is felkínálnak a szénszálak pozicionálására. A futócipő prototípusát olyan sportolóknak tervezték, akik városokban futnak nagy sebességgel.
A Strung technológiával készített cipők felsőrészei egy darabból állnak, ami igencsak megkönnyíti a gyártást. Nincsenek különböző szövet-, bőr- és műanyagrészek, amiket össze kéne varrni. A Strung csapata szerint a gyártósori gép percek alatt előállíthatja egy-egy cipő felsőrészét. A tervezett széria legyártásához ezért nincs szükség komplex gyártósorokra, csak 10 cipőnyomtató robotra. És nemcsak a gyártás könnyű, hanem maga a cipő is: a Strung futócipők felsőrészének tömege csupán 35 gramm.
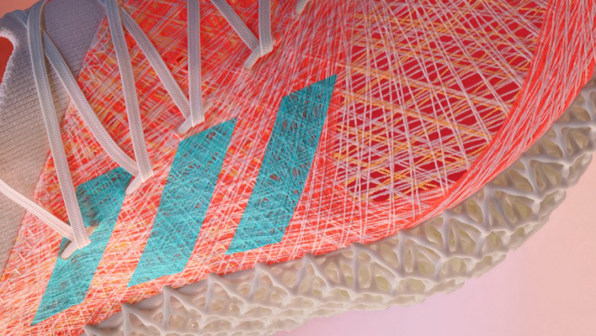
A Strung szöveteket az Adidas nemcsak futócipőkben, hanem más termékeiben is fel fogja használni. Az első cipők legkorábban 2021 végén, de inkább 2022 végén kerülhetnek a boltokba.
Kapcsolódó cikkek a Qubiten: