A nehézipar reformja nélkül meddő a klímaváltozás elleni harc, de már megvan a csodaszer: a zöld acél

Ha a klímaváltozásnak lenne zászlaja, és csak egyetlen anyag lehetne a címerében, valószínűleg az acélra esne a választás. Az üvegházhatású gázok kibocsátásának több mint 73 százalékáért az energiafogyasztás (áram, fűtés, közlekedés) felel, ezen belül is a legnagyobb mértékben az ipari fogyasztás, a gyártás, és ha még tovább bontjuk ezt a kategóriát, akkor a vas- és acélipar áll az élen, ami a világ teljes kibocsátásának 7,2 százalékát produkálja.
Az acél a modern gazdaság alapját képezi: szilárdsága, szívóssága és alacsony előállítási költségei miatt ott van az épületekben, a hidakban, az óceánjáró hajókban, a vonatokban, az autókban, a háztartási eszközökben és a fegyverekben is. Az évente közel 2 milliárd tonna nyersacélt termelő globális acélipar éves forgalma 2,5 billió (2500 milliárd) dollár körül mozog, miközben az anyag előállítása során több milliárd tonna szén-dioxidot bocsátanak a légkörbe.
„Elég nagy az egyetértés abban, hogy ha tényleg hozzá akarunk járulni ahhoz, hogy megvalósítsuk a párizsi egyezményben foglalt klímacélokat, akkor már nem elég tovább javítani a nagyolvasztók hatékonyságát, hanem áttörő technológiákra van szükség, méghozzá sürgősen” – mondta a Financial Timesnak Martin Pei, a SSAB nevű svéd acélgyártó cég technológiai vezetője.
A SSAB az elmúlt években partnereivel (az LKAB bányatársasággal és a Vattenfall energiaipari multival) együtt létrehozta a Hybrit nevű projektet, amelynek keretében azon dolgoznak, hogy megteremtsék a fosszilis energiahordozóktól mentes acélgyártás alapjait. Ez már csak azért is óriási kihívás, mert az acélgyártáshoz nyersvas szükséges, a nyersvasgyártás folyamata pedig azzal kezdődik, hogy a vasércből eltávolítják az oxigént, amit hagyományosan szén égetésével oldanak meg – ezt hívják redukciónak, és ebből ered a jelentős szén-dioxid-kibocsátás.
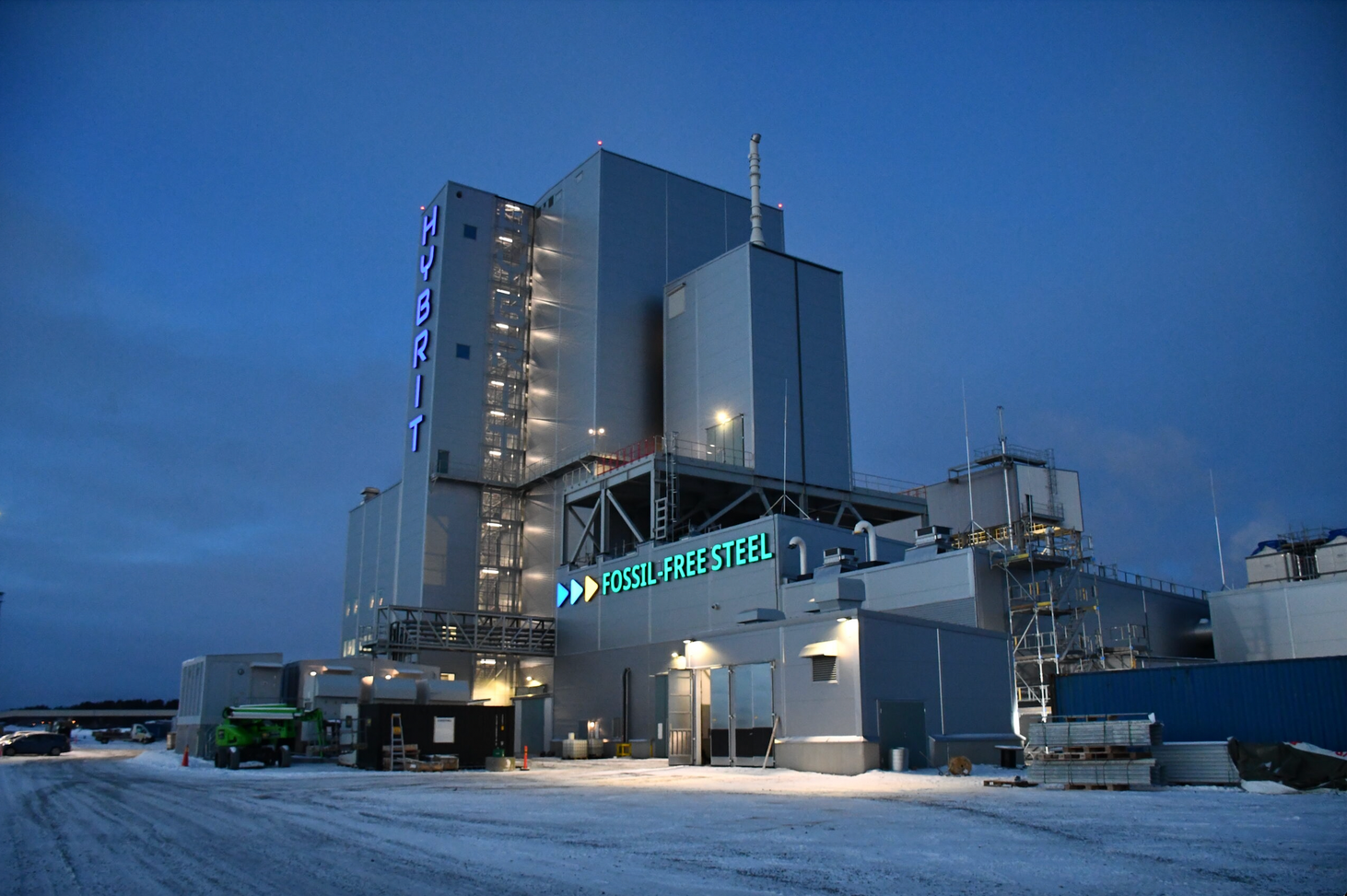
A Hybrit ebből a képletből vette ki a szenet, és hidrogénnel helyettesítette: a redukcióhoz szükséges hidrogéngázt ráadásul megújuló energiaforrások használatával állítják elő.
A szén nehezen pótolható, és drágább is lesz az acél nélküle
A Nemzetközi Energiaügynökség számításai szerint ahhoz, hogy elérjük a kitűzött globális klímacélokat, az acélipar szén-dioxid-kibocsátását legalább a felére kell csökkenteni 2050-ig, de utána is fokozatosan a zéró kibocsátás felé kell haladni. A Financial Timesnak nyilatkozó fenntarthatósági szakértők szerint a technológiai fejlődés ezen a téren is biztató, és akár már 2030-ra láthatjuk a közel zéró kibocsátású gyárak első hullámát – és ebben hatalmas szerepe lesz a hidrogénnek.
Az átállás persze eleinte költséges lesz. Európa és a teljes nyugati világ legnagyobb acélgyártó vállalata, a luxemburgi székhelyű ArcelorMittal becslései szerint a saját üzemeinek dekarbonizálása – az EU klímacéljainak megfelelő mértékben – valahol 15 és 40 milliárd euró közötti összegbe kerül majd a cégnek. Ha azt nézzük, hogy a vállalat az előző negyedévben közel 3,5 milliárd euró profitot termelt, ezt a befektetést akár barátinak is lehetne tekinteni, de az acélipar híresen volatilis: az elmúlt években volt már olyan negyedév is, amit 5,6 milliárdos veszteséggel zártak. Lakshmi Mittal, a vállalatot vezető indiai acélmágnás figyelmeztetett is rá: „Ezek a technológiák megemelik majd az acélunk árát. Nem lesz olcsó, a fogyasztóknak fel kell készülni a költségekre.”
Az acél a vas ötvözete, 98-99 százalékban nyersvasat tartalmaz, így az acélipar legfőbb kibocsátása a nyersvasgyártás során történik. A bányászott vasércet 1000 Celsius-foknál is forróbbra felmelegített nagyolvasztókba helyezik, a szénből előállított koksszal és salakképző anyagokkal (pl. mészkő) együtt. A vasérc és koksz égése során a koksz szén-monoxiddá alakul, a vasérc pedig fémmé redukálódik, és folyékony állapotban távozik a kemencéből. A szén-dioxid a folyamat melléktermékeként kerül a légkörbe. Ez meglehetősen nagy energiaigényű folyamat, amelyhez messze a szénalapú koksz a legköltséghatékonyabb tüzelőanyag, amit ráadásul kedvező tulajdonságai, például nagy hőfejlesztő képessége miatt is nehéz pótolni.
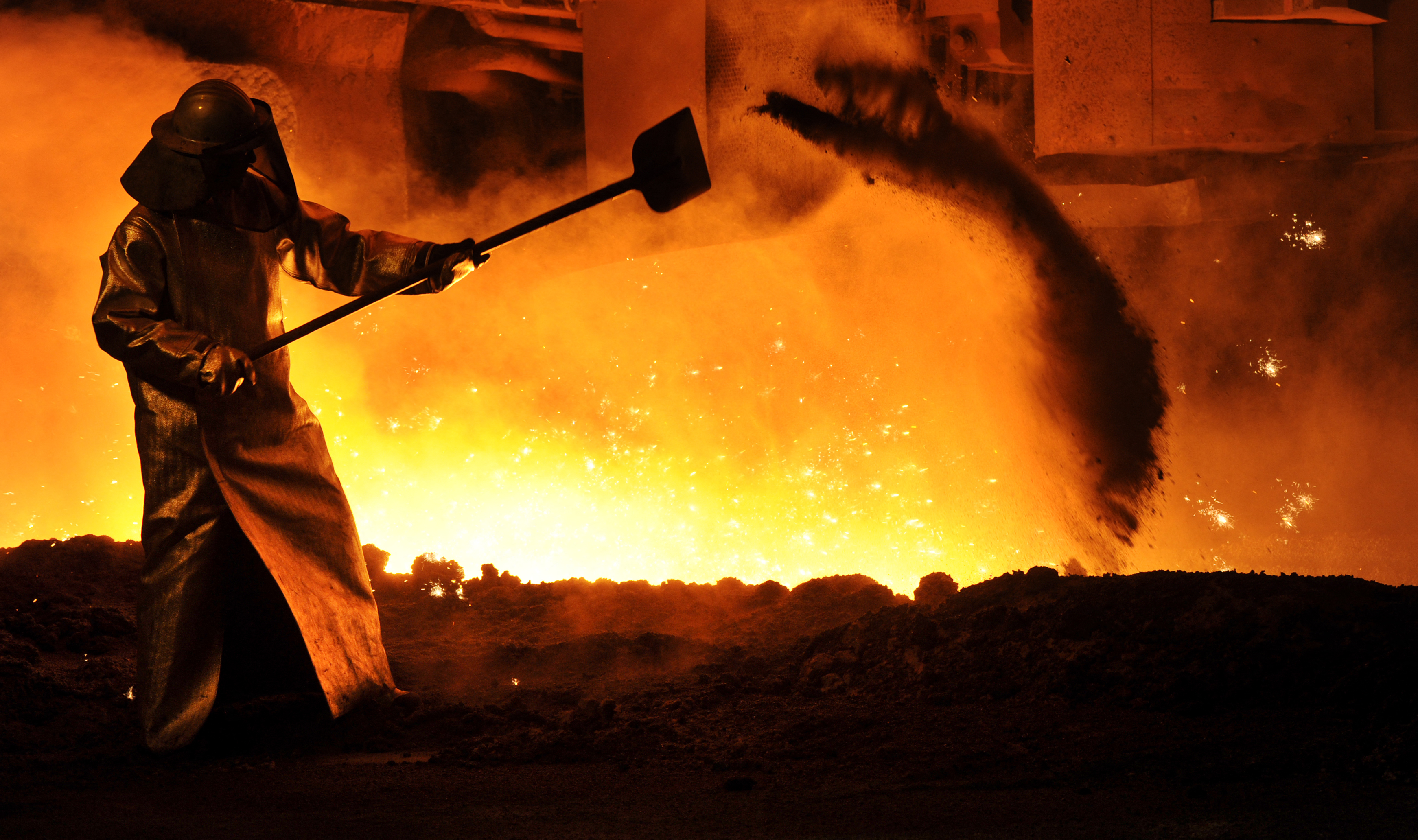
A SSAB észak-svédországi próbaüzemében az elmúlt hónapokban kezdtek kísérletezni az évszázados acélgyártási hagyományokat forradalmasító technológiával. A cég ígéretei szerint a vasérc hidrogéngázzal való redukálása során gyakorlatilag zéró szén-dioxid-kibocsátással kell számolni, és a vízgőz az egyetlen melléktermék – a hidrogéngázt egy elektrolízis-üzemben állítják elő, amit Svédország bőséges megújuló energiaforrásai működtetnek. Az így létrejövő vasszivacsot hulladékacéllal együtt helyezik az ívkemencébe, és kész az elektroacél.
A SSAB, amely az ArcelorMittal és az osztrák Voestalpine fő versenytársa a zöld acél gyártásában, két dolgot jelölt meg abszolút prioritásként a szénzabáló nagyolvasztóktól való elfordulás folyamatában: az elektrolízises gyártás felskálázását és a hidrogéngáz árammal történő előállításának olcsóbbá tételét. A vállalat becslései szerint az így előállított acél eleinte 20-30 százalékkal lesz drágább.
„Beszéltünk az acélipari vásárlóinkkal, de ők nem voltak annyira oda az ötletért, hogy többet fizessenek a zöld acélért. Aztán beszéltünk a vásárlóink vásárlóival, őket viszont nagyon is érdekelte a dolog” – mondta a Canary Mediának az LKAB bányatársaság energia- és klímaügyi alelnöke, Stefan Savonen.
Az LKAB észrevételei szerint az európai autó- és kamiongyártók például elkötelezettek a zöld acél iránt, és egymással versenyeznek azért, hogy úttörői legyenek a technológiai váltásnak. A H2 Green Steel nevű svéd konzorcium márciusban a Volkswagen-csoporthoz tartozó Scaniával, májusban a Mercedes-Benzzel állapodott meg, és mindkét cég vállalta, hogy 2025-ig elkezdi beépíteni a karbonmentes folyamattal előállított acélt a járműveibe, és a teljes karbonmentesség elérésének határidejét is megállapították – a Scania 2028-ra, a Mercedes 2039-re érné el a zéró kibocsátású gyártást.
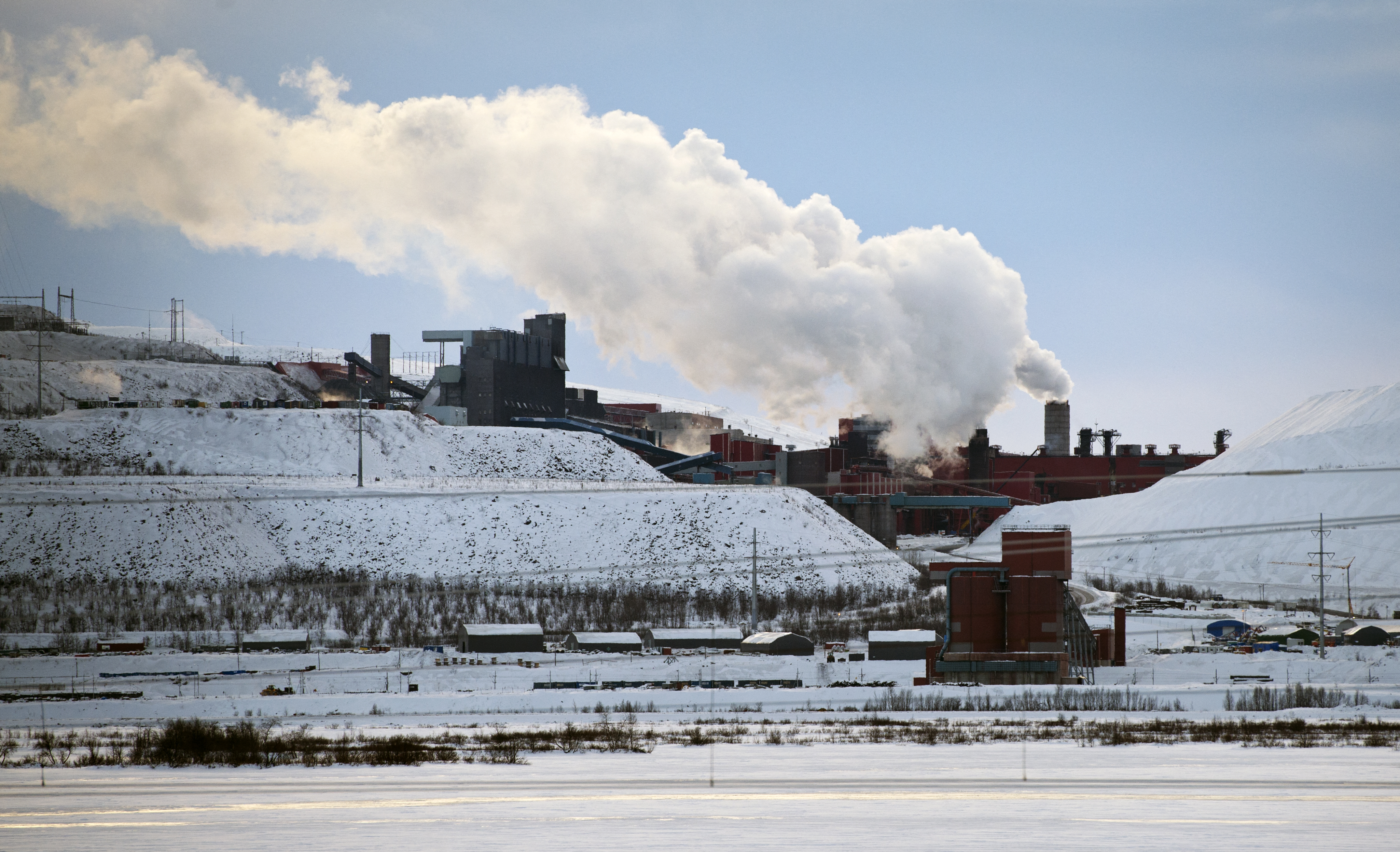
Azonban így is a Hybrit lett az első olyan cég, amely leszállította az első adag zöld acélt. Miután áprilisban bejelentették a Volvo Grouppal való együttműködést, és az autógyártó kijelentette, hogy 2026-ra a világon elsőként szeretne átállni a zöld acélból készült járművek tömeggyártására, az elsősorban kamionokat gyártó cég augusztus második felében kézhez is kapta az első szállítmányt. A Volvo Group még idén elkezdené a prototípusok gyártását a vadiúj alapanyagból.
Ha lehet hinni Kínának, akkor globálisan sincs miért aggódni
Miközben az uniós Green Deal értelmében az európai acélipart egyre inkább fenyegetik a magas szénadók és a dekarbonizációs szabályozások, a kapcsolódó területeken is akcióba lendültek: tíz nagy európai építőipari és ingatlankezelő cég megalapította a SteelZero koalíciót, amivel szintén elkötelezték magukat amellett, hogy 2050-ig teljesen megszabadítják működésüket a fosszilis energiahordozóktól. „A piac már készen áll, de egyelőre nincs, aki ellássa. A piac a gyártókra vár” – mondta Savonen, aki szerint ezek a gyártók a Green Dealnek köszönhetően hamar meg fognak jelenni.
Miután tehát az elmúlt egy évben a világ legnagyobb acélgyártói beálltak a párizsi klímaegyezményben megfogalmazott célok mögé, valamint az Európai Unió és Joe Biden megválasztása után az Egyesült Államok is rákapcsolt a zöld gazdaság elérésére különböző szabályozások és ösztönzők útján, marad a kérdés, hogy mi lesz a világ acélgyártásának több mint felét adó Kínával. Hszi Csin-ping ugyanakkor még tavaly bejelentette, hogy Kína 2060-ra teljesen karbonsemlegessé válik, és ennek az állam cégei is igyekeznek megfelelni.
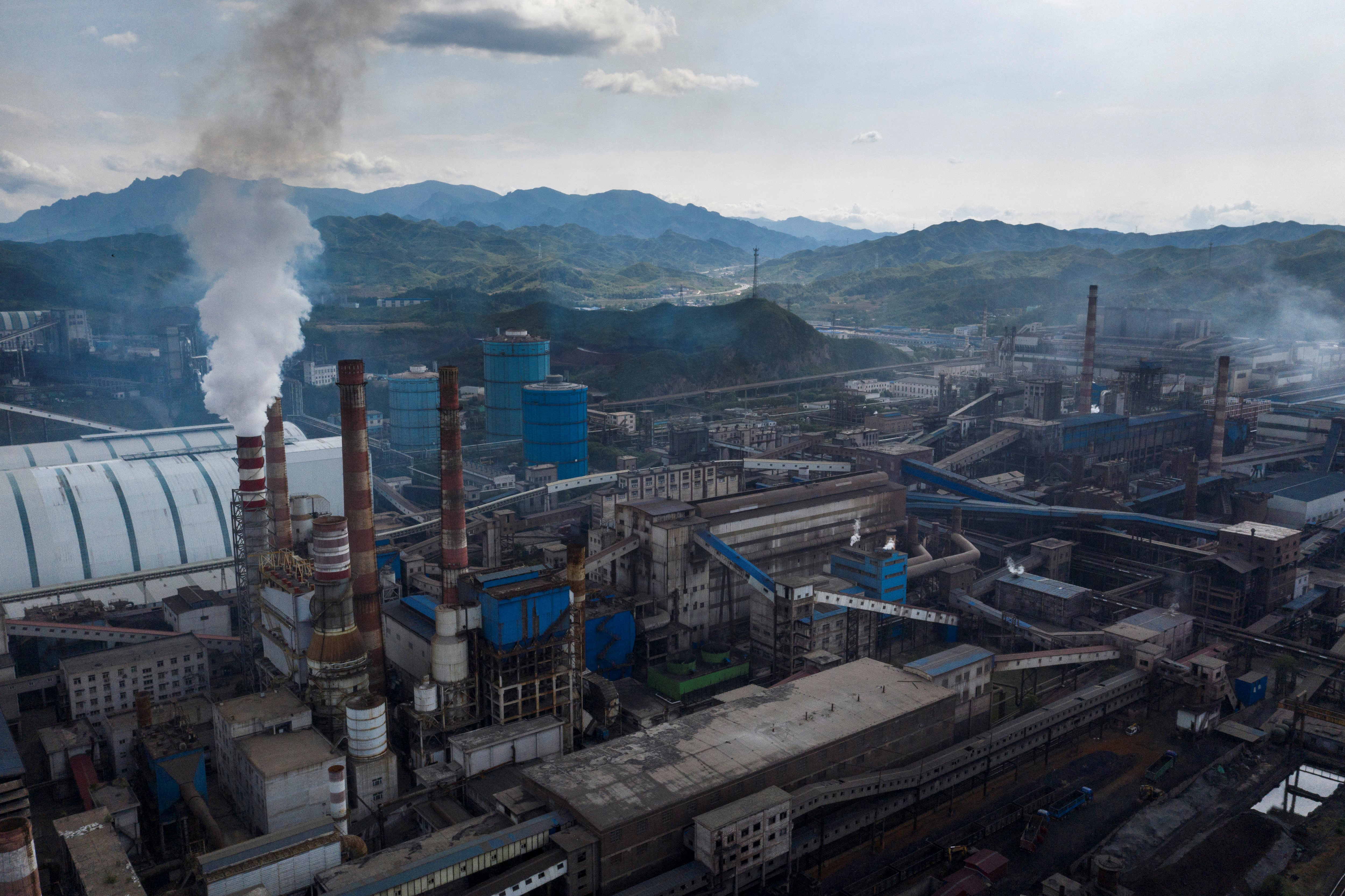
A világ legnagyobb acélgyártója, az állami tulajdonban lévő sanghaji Baowu Steel Group például már egy évtizeddel korábbra, 2050-re megígérte a karbonsemlegességet, ami elengedhetetlen lesz a pekingi célok eléréséhez: a kínai szén-dioxid kibocsátás csúcsértékét már 2025 előtt szeretnék elérni, hogy 2030-ra már 30 százalékos csökkenést jelenthessen az ország. Az elemzők szerint hiába ambiciózus célok ezek – ha valahol meg lehet valósítani egy ilyen, a teljes ipart érintő váltást, akkor az a központi vezérlésű kommunista állam, Kína.
Kapcsolódó cikkek a Qubiten: